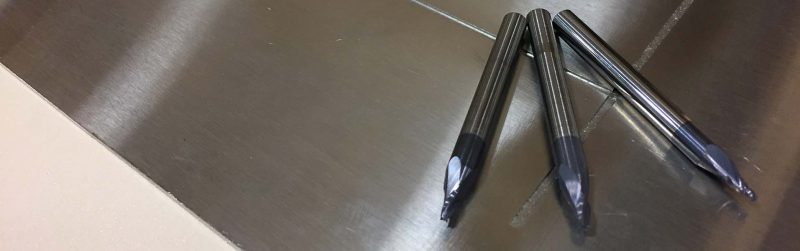
How to Mill Scoring Channels in a Steel Thinplate
In the last few years, there have been some drastic developments in not only steel for thinplates but also for the milling bits. These developments have slashed the amount of time it takes to mill a steel plate to where it now takes far less time to mill a plate than it does to rout a set of phenolics. What once took hours to produce on steel can now be completed in a fraction of that time.
Some just look at the cost of a sheet of phenolic compared to a steel plate and on just that level, the phenolic is less expensive. But factor in the milling time; the finishing time of cleaning up edges on the counterplates, setting the counterplates onto the cut plate, the additional make ready that could be required because of the amount of draw over all the counterplates. Now compare that with the alternative, milling the channels, wire brush and spray clean the channels, mounting the thinplate, aligning the cut, and go. The material costs are not what leads to lost profits, it’s the lost time on press that reduces bottom lines. So, want to increase your profits? Make the switch to PowerPlates.
The best way to mill a PowerPlate is to position it on the table using an X, Y guide to make sure the plate is squared to those axis’ and that there is a 0,0 point to work off of. For example, with a Gerber Profile use the rails to locate the corner of the plate at 0,0. Run a strip of blue painter’s tape all around the edge of the plate where the tape is half on the plate and half on the table. Mask off the rest of the table so the vacuum is not lost. With an aerosol WD40, spray a fine mist over the entire surface for lubrication. If a cold air gun is attached use it. It’s not absolutely necessary but it will extend the life of the bit and reduce the amount of cleanup on the edges of the channels.
With Essential Products Channel Bits and PowerPlates, at 40k RPM set the plunge at 15 ipm, cutting speed at 300 ipm, and depth per pass of .003. Once completed, use an orbital sander to run along the channels to knock off any burr that might be on the edge of the channels. If no cold air gun was used it’s also a good idea to use a wire brush afterward to further smooth the edges. Brake shoe cleaner works extremely well for cleaning off the plate once it is complete. Once you’re done, it’s time to go to press.
Back To Blog